hydroranger 200 user manual
Summary
Get the comprehensive Hydroranger 200 User Manual! Learn installation, maintenance, and troubleshooting tips. Download now for easy setup and optimal performance.
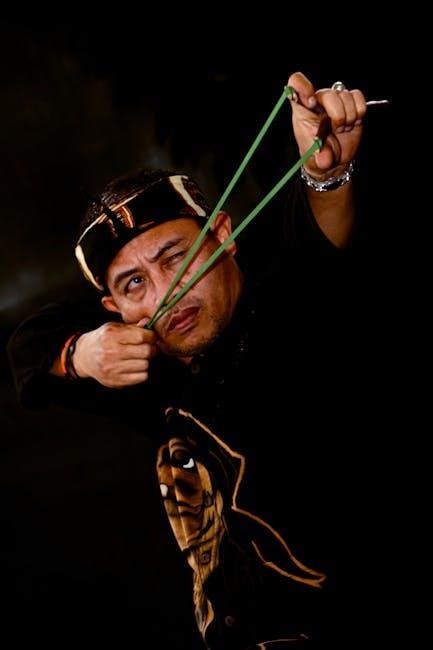
The HydroRanger 200 is a non-contact ultrasonic level transmitter designed for measuring liquid levels in tanks, wells, and flumes. It offers reliable performance and versatility.
1.1 Overview of the Device
The HydroRanger 200 is a non-contact ultrasonic level transmitter designed for measuring liquid levels in tanks, wells, and open channels. It utilizes advanced ultrasonic technology to provide accurate and reliable measurements. The device is suitable for various applications, including water treatment, chemical storage, and industrial processes; Its compact design and ease of installation make it a popular choice for level monitoring systems.
1.2 Key Features and Benefits
The HydroRanger 200 features non-contact ultrasonic technology for precise level measurement. It supports digital communication via Modbus RTU and is compatible with SmartLinx and SIMATIC PDM systems. The device offers an intuitive HMI for easy configuration and operation. Its robust design ensures reliability in harsh environments, while low maintenance requirements enhance operational efficiency. These features make it ideal for water treatment, chemical storage, and industrial applications.
Safety Guidelines and Precautions
Adhere to safety guidelines to ensure personal and property safety. Observe all warning notices and precautions to prevent accidents and device damage during installation and operation.
2.1 General Safety Precautions
Always follow general safety precautions when handling the HydroRanger 200. Ensure proper grounding and avoid exposure to hazardous environments. Do not open the device while it is powered on, and use approved tools for any adjustments. Personal protective equipment should be worn during installation and maintenance. Failure to comply may result in injury or equipment damage.
2.2 Hazardous Area Considerations
When installing the HydroRanger 200 in hazardous areas, ensure compliance with local explosion-proof regulations. Use appropriate intrinsic safety barriers and verify device certification for such environments. Avoid sparking tools and follow proper grounding procedures to prevent ignition risks. Always consult the manual for specific guidelines on hazardous area installations to ensure safe operation and compliance with industry standards.
Installation and Setup
Ensure proper site preparation and follow installation guidelines for the HydroRanger 200. Mount the device securely, aligning it correctly for accurate measurements. Refer to the manual for detailed setup instructions and electrical connections to ensure reliable operation.
3.1 Site Preparation and Requirements
Ensure the installation site is stable, level, and free from vibrations. Select a location with minimal interference and optimal ultrasonic signal clarity. Maintain adequate space for maintenance access. Verify electrical requirements and ensure proper grounding. Consult the manual for specific environmental considerations and safety guidelines to guarantee compliance and reliable operation.
3.2 Mounting and Alignment of the Device
Mount the HydroRanger 200 securely on a stable, level surface using approved hardware. Ensure the transducer is aligned perpendicularly to the liquid surface. Verify proper alignment to avoid obstructions and ensure accurate ultrasonic signal transmission. Use a spirit level to confirm the device is correctly positioned. Tighten mounting hardware according to torque specifications to prevent vibration or movement, ensuring reliable performance and accurate measurements.
Operating the HydroRanger 200
The device operates in RUN and PROGRAM modes, enabling real-time level measurement and configuration adjustments. RUN mode provides continuous monitoring, while PROGRAM mode allows parameter customization for tailored operation.
4.1 RUN Mode Operation
The HydroRanger 200 in RUN mode continuously measures and displays liquid levels, providing real-time data for monitoring applications. This mode is designed for uninterrupted operation, ensuring accurate and reliable measurements. The device automatically updates level readings, making it ideal for applications requiring constant oversight. Users can view current levels on the display and rely on its non-contact ultrasonic technology for consistent performance in various environments.
4.2 PROGRAM Mode Operation
In PROGRAM mode, the HydroRanger 200 allows users to configure settings such as output scaling, measurement range, and alarm thresholds. This mode enables customization of the device to meet specific application requirements. Accessing PROGRAM mode typically requires a password to ensure secure configuration. Once configured, the device stores these settings and operates according to the defined parameters, ensuring tailored performance for precise level measurement and control applications.
Configuration and Settings
The HydroRanger 200 offers customizable settings, including mA output range adjustment and digital communication configuration, ensuring tailored performance for specific applications and seamless integration with control systems.
5.1 Adjusting the mA Output Range
To adjust the mA output range on the HydroRanger 200, access the configuration menu via the HMI. Select the mA RANGE parameter and input the desired span. Use the P214 parameter to set the zero point. Ensure the output matches your control system requirements for accurate level measurement. Refer to the manual for detailed calibration steps to avoid measurement errors.
5.2 Configuring Digital Communications
Configure digital communications on the HydroRanger 200 via the Modbus RTU protocol using RS-485. Set the baud rate, parity, and address in the device settings. Ensure compatibility with your control system. Refer to the manual for specific instructions to enable seamless integration with systems like SmartLinx or SIMATIC PDM, ensuring accurate data transmission and control.
Maintenance and Troubleshooting
Perform routine checks, clean the transducer, and verify electrical connections. Troubleshoot issues like faulty readings or communication errors. Refer to the manual for detailed procedures.
6.1 Routine Maintenance Procedures
Regular maintenance ensures optimal performance. Clean the transducer with a soft cloth and avoid harsh chemicals. Check electrical connections and verify output settings. Inspect for damage or wear. Perform calibration checks as needed. Ensure proper alignment and adjust if necessary. Refer to the manual for detailed procedures and schedules to maintain accuracy and reliability.
6.2 Common Issues and Solutions
Common issues include incorrect measurements, communication errors, or sensor malfunctions. Verify alignment and cleanliness of the transducer. Check electrical connections and settings. For communication issues, ensure proper Modbus configuration. Resetting to factory settings may resolve software glitches. Refer to the manual for troubleshooting guides and contact support for persistent problems. Regular maintenance can prevent many issues.
Technical Specifications
The HydroRanger 200 operates using ultrasonic technology, measuring up to 15 meters with ±10mm accuracy. It functions in temperatures from -40°C to 60°C, with a 4-20mA output and Modbus RTU communication.
7.1 Performance Characteristics
The HydroRanger 200 offers precise ultrasonic level measurement with a range of up to 15 meters and accuracy of ±10mm. It operates effectively in temperatures from -40°C to 60°C, ensuring reliability in diverse environments. The device supports a 4-20mA output and features Modbus RTU communication for seamless integration with control systems, enhancing its versatility in various industrial applications.
7.2 Compatibility with Other Systems
The HydroRanger 200 is compatible with the SmartLinx system and SIMATIC PDM for advanced integration. It supports Modbus RTU communication via RS-485, enabling connectivity with industrial control systems. The device works seamlessly with various materials, including water, waste, and high-angle applications, making it versatile for diverse industrial setups and ensuring efficient data exchange across compatible platforms.
Compliance and Certifications
The HydroRanger 200 complies with industry standards and certifications, ensuring reliable performance. It is backed by a 24-month warranty, reflecting its commitment to quality and durability.
8.1 Industry Standards and Certifications
The HydroRanger 200 complies with global industry standards, ensuring safety and reliability. It meets CE and FM certifications, adhering to stringent safety and environmental regulations. Designed under Siemens Milltronics, it is built to withstand harsh conditions and is compatible with systems like SmartLinx and SIMATIC PDM. The device also carries a 24-month warranty, reflecting its commitment to quality and durability.
8.2 Warranty Information
The HydroRanger 200 is covered by a 24-month warranty, ensuring protection against manufacturing defects. Repairs or replacements are provided during this period, excluding damages from misuse or unauthorized modifications. Warranty details are outlined in the manual, with options for extended coverage available for added protection.
Accessories and Additional Equipment
Recommended accessories include mounting brackets, cables, and adapters for seamless integration. Additional software tools enhance configuration and monitoring capabilities, ensuring optimal performance and ease of use.
9.1 Recommended Accessories
Essential accessories for the HydroRanger 200 include mounting brackets for secure installation, high-quality cables for reliable connections, and adapters for seamless integration with existing systems. Additional hardware, such as external power supplies or signal conditioners, may be required for specific applications. These accessories ensure optimal performance, ease of use, and compatibility with various industrial setups, enhancing the device’s functionality in diverse environments.
9.2 Optional Software and Tools
Optional software includes the Process Device Manager (PDM) for advanced configuration and monitoring; The SmartLinx system provides enhanced integration capabilities. Additional tools like the HMI (Human Machine Interface) module and communication adapters enable seamless connectivity. These software solutions and tools enhance functionality, allowing for remote monitoring and customization of the HydroRanger 200 to meet specific application requirements.
Compatibility with Other Devices
The HydroRanger 200 seamlessly integrates with systems like SmartLinx and SIMATIC PDM. It supports Modbus RTU via RS-485, ensuring compatibility with various industrial devices and control systems.
10.1 Integration with SmartLinx System
The HydroRanger 200 integrates seamlessly with the SmartLinx system, enabling advanced control and monitoring of liquid levels. This integration allows for centralized configuration and real-time data acquisition. Users can access detailed parameter settings and monitor performance efficiently. The SmartLinx system enhances the device’s functionality, ensuring optimal performance in various industrial applications. For detailed setup instructions, refer to the SmartLinx system manual.
10.2 Compatibility with SIMATIC PDM
The HydroRanger 200 is fully compatible with SIMATIC PDM, enabling comprehensive device management and diagnostics. Through PDM, users can configure settings, monitor performance, and perform routine maintenance tasks. This compatibility ensures seamless integration into Siemens-based systems, enhancing operational efficiency and simplifying device management. The PDM software provides tools for troubleshooting and optimizing the HydroRanger 200’s operation in industrial environments.
Digital Communication and Control
The HydroRanger 200 offers digital communication via Modbus RTU over RS-485, facilitating remote monitoring and control of level measurements in industrial automation systems efficiently.
11.1 Modbus RTU via RS-485
The HydroRanger 200 supports Modbus RTU communication over RS-485, enabling seamless integration with industrial systems. This protocol allows for efficient data exchange, including level measurements, diagnostic information, and configuration commands. The device can be set up as a slave unit, responding to master requests. It ensures reliable and efficient communication in various monitoring and control applications.
11.2 Monitoring Wet Wells, Weirs, and Flumes
The HydroRanger 200 is ideal for monitoring liquid levels in wet wells, weirs, and flumes. Its non-contact ultrasonic technology ensures accurate measurements without interference from floating debris or turbulent surfaces. Suitable for water, wastewater, and industrial applications, it provides reliable data for flow calculation and control. The device supports efficient management of pumping systems and water resources in various municipal and industrial settings.
Refer to the full HydroRanger 200 manual for detailed insights. The device is covered by a 24-month warranty, ensuring reliable performance and support for its users.
12.1 Final Tips for Optimal Use
- Regularly inspect and clean the transducer to ensure accurate measurements.
- Follow the maintenance schedule outlined in the manual for optimal performance.
- Use only genuine Siemens accessories to maintain reliability and compatibility.
- Monitor wet wells, weirs, and flumes to prevent unexpected operational issues.
- Utilize digital communication features like Modbus RTU for seamless integration.
- Refer to the HydroRanger 200 manual for troubleshooting common issues promptly.
12.2 Downloading the Full Manual
To access the complete HydroRanger 200 manual, visit the official Siemens website. Navigate to the support section, where you can search for the device by name. Select the HydroRanger 200 option and choose the PDF format. The manual is available for free download without registration, ensuring easy access to detailed instructions, specifications, and troubleshooting guides.